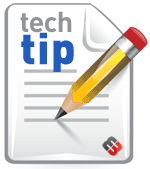
Viscosity is a key criterion in the epoxy selection process, for many bonding, sealing, coating, and potting applications. Master Bond epoxy adhesives are formulated in low, medium, and high / non-drip viscosities. Low viscosity systems excel in many kinds of applications, including potting, encapsulation, and impregnation. Moderate viscosity products offer convenient dispensing, and are widely used in many bonding and sealing applications. High viscosity pastes are noted for their non-drip or non-sagging properties, and are used in applications where the epoxy needs to stay in its place while applying and curing.
Viscosity and modes of flow
Viscosity may be simply defined as the resistance to flow, of a liquid. Fluids are broadly classified as: Newtonian Fluids and Non-Newtonian fluids. In Newtonian fluids, the viscosity doesn’t depend on the shear rate, whereas in Non-Newtonian fluids, the viscosity changes based on the shear rate. Most of the epoxy resin compounds, like the great majority of other polymer systems, fall into the Non-Newtonian category.
Sample of low, moderate and high (non-drip) viscosity epoxies. Notice how each sample settles differently according to its viscosity.
Measuring viscosity
There are many test methods and instruments available, for measuring the viscosity of materials. One of the most widely used instruments for viscosity tests is the Brookfield viscometer which can determine the viscosity as a function of shear rate, time, and temperature. Different types of Brookfield viscometers and accessories are available, depending on the range of the viscosity being measured. Two widely used units of measurements for viscosity are: Centipoise (cps) and Pascal-second (Pa-s).
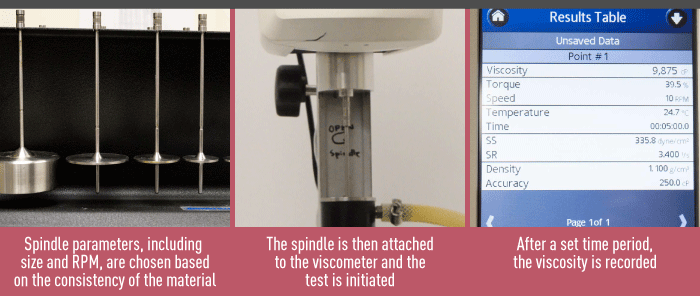
Photo of spindles & viscometer.
Viscosity of common materials
The table below lists the viscosities of common fluids and solids at 75°F in cps:
Typical Viscosities of Common Fluids | |
---|---|
Liquid Name | Viscosity, cps, at 75°F |
Water | 1 |
SAE 30 motor oil | 250 |
Maple syrup | 3,000 |
Honey | 10,000-20,000 |
Ketchup | 30,000-50,000 |
Peanut butter | > 250,000 |
Window putty | >5,000,000 |
An epoxy’s viscosity defines the applications (such as bonding, sealing, potting etc.) that it can be used for, as well as the means by which it can be applied. Master Bond epoxy compounds are available in a very wide range of viscosities from as low as 100 cps to in excess of 1,500,000 cps for various bonding, coating, sealing and potting applications.
Some examples are our products EP30LV-1, EP62-1LPSP, and Supreme 112, which have extremely low viscosities and excellent wicking capabilities, for filling tiny gaps. Products such as EP21TDCHT-LO and Supreme 10HTCL have a moderately flowable viscosity, whereas Supreme 10HTND-3, Supreme 3HTND-2DM-1, and EP17HTDM-2 Black offer a non-drip paste consistency, for applications where no flow is desired.
Find out more about our adhesives with different viscosities.
Low, Moderate and High Viscosity Systems
![]() |
EP30LV-1 Ultra low viscosity epoxy system. Cures at room temperature. Outstanding optical clarity. Electrically insulative. High strength rigid bonds. Fills gaps in confined areas. Serviceable from -60°F to +250°F. |
![]() |
EP62-1LPSP Low viscosity, optically clear epoxy with superior electrical insulation properties. Thermal stability. Exceptional chemical resistance. Long working life. Low exotherm. Withstands 1,000 hours 85°C/85% RH. Meets NASA low outgassing specifications. Serviceable from 4K to +400°F. |
![]() |
Supreme 112 Potting, encapsulation, coating, sealing, impregnation compound. Low viscosity, long working life. Superior physical strength. Serviceable from -80°F to 550°F. |
![]() |
EP21TDCHT-LO Two component, toughened epoxy adhesive. High peel strength and shock resistant. NASA low outgassing certified. Convenient one to one mix ratio. Ideal for bonding similar and dissimilar substrates. Withstands 1,000 hours 85°C/85% RH. Serviceable from -100°F to +350°F. Good flow. Easy to apply. |
![]() |
Supreme 10HTCL Single component toughened epoxy adhesive with good flow properties. Resistant to thermal cycling, mechanical vibration/shock. Tensile lap shear strength 2,800-3,000 psi. T-peel strength 25-30 pli. Cures in 60-75 minutes at 250°F, shorter times at higher temperatures. Successfully tested at 1,000 hours 85°C/85% RH. Serviceable from 4k to +400°F. |
![]() |
Supreme 3HTND-2DM-1 Toughened epoxy system for bonding, sealing and specialty dam-and-fill encapsulation. Requires no mixing. Rapid heat curing. Passes NASA low outgassing testing. Transfers heat efficiently. Stellar electrical insulation properties. Serviceable from -100°F to +400°F. |
![]() |
EP17HTDM-2 Black One component, heat cured epoxy for bonding and sealing, as well as die attach applications. Flowable, high viscosity system, cures in 4-6 hours at 300°F or 2-3 hours at 350°F. Post curing at 400°F for 1-2 hours to optimize properties. Limited flow and low exotherm when curing. |